[Customized Spare Parts for Tube Mills]Unlocking Efficiency in Manufacturing: The Importance of Customized Spare Parts for Tube Mills in Modern Production Processes
In today’s fast-paced manufacturing environment, efficiency is paramount. For industries relying on tube milling processes, the availability and quality of spare parts can significantly impact overall productivity. Customized spare parts for tube mills have emerged as a critical solution to enhance operational efficiency, minimize downtime, and adapt to the unique requirements of various manufacturing setups. This article explores the significance of tailored spare parts and their role in ensuring that tube mills perform at their best.
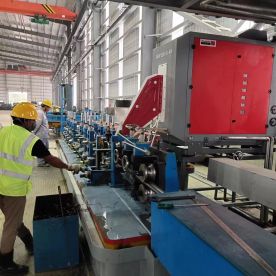
Unlocking Efficiency in Manufacturing: The Importance of Customized Spare Parts for Tube Mills in Modern Production Processes
Understanding Tube Mills and Their Importance
Tube mills are essential machinery in several sectors, including automotive, construction, and furniture, where they are used to produce pipes and tubes from metal sheets. The efficiency and quality of the produced tubes directly correlate with the performance of these mills. A well-maintained tube mill allows for high-speed production while minimizing material waste. However, like any industrial machinery, tube mills require regular maintenance and replacement of worn or damaged parts.
The Need for Customized Spare Parts
One-size-fits-all solutions are often inadequate in the high-stakes world of manufacturing. Each tube mill can have unique specifications based on the materials being processed, the intended application, and the operational environment. Customized spare parts are designed to meet these specific requirements, leading to numerous advantages:
1. **Enhanced Compatibility**: Customized spare parts ensure compatibility with existing equipment. They are engineered to fit perfectly with the specific models of tube mills, reducing the risks of malfunctions or poor performance.
2. **Improved Performance**: By utilizing parts tailored for specific machines, manufacturers can significantly enhance the operational performance of their tube mills. This customization often leads to improved speed, better accuracy in production, and higher quality end products.
3. **Increased Longevity**: When spare parts are specifically designed for a particular tube mill, they tend to exhibit greater durability. This longevity helps in reducing the frequency of replacements, which can carry substantial costs over time.
4. **Cost-effectiveness**: Although custom parts may come with a slightly higher upfront cost compared to generic solutions, the long-term savings achieved through reduced downtime and increased efficiency can be substantial. Customized parts minimize the risk of breakdowns, leading to uninterrupted production cycles.
5. **Rapid Problem Solving**: Customized spare parts can often be developed faster than generic replacements can be sourced, allowing manufacturers to address issues without the prolonged downtime that comes from waiting on third-party suppliers.
Implementing Customized Spare Parts Solutions
To benefit from customized spare parts for tube mills, manufacturers must adopt a strategic approach. The first step is to conduct a thorough analysis of the machinery and identify the parts that require customization. Regular maintenance checks and monitoring of the tube mill’s performance can reveal which components are most susceptible to wear and tear.
Collaboration with manufacturers and suppliers who specialize in custom parts is another crucial step. These experts can provide insights into the latest materials and technologies that may enhance the design and durability of the spare parts. Engaging with suppliers who can offer quick turnaround times is also beneficial, ensuring parts are available as needed.
Furthermore, investing in technology like predictive maintenance tools can lead to proactive measures for managing spare parts inventory. By understanding the expected timing of wear, manufacturers can arrange for custom replacements before any significant issues arise.
Case Studies: Success Stories with Customized Spare Parts
Numerous manufacturers have already reaped the rewards of investing in customized spare parts for tube mills. For instance, a prominent automotive parts manufacturer redesigned its tube mill with tailored components, resulting in a 25% increase in production speed and a notable reduction in waste material. Another case involved a construction company that faced frequent breakdowns due to generic parts drainage. Once they transitioned to customized solutions, their operational efficiency improved dramatically, leading to increased project capacity.
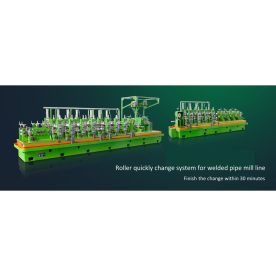
Unlocking Efficiency in Manufacturing: The Importance of Customized Spare Parts for Tube Mills in Modern Production Processes

Unlocking Efficiency in Manufacturing: The Importance of Customized Spare Parts for Tube Mills in Modern Production Processes
Conclusion
In conclusion, customized spare parts for tube mills are not merely an option; they are a necessity for manufacturers looking to stay competitive in a rapidly evolving industry. The alignment of spare parts with the specific needs of tube mills fosters enhanced efficiency, reduced downtime, and ultimately, better returns on investment. By prioritizing customized solutions, companies can ensure that their manufacturing processes remain agile, cost-effective, and capable of meeting market demands. As the landscape of manufacturing continues to advance, the strategic use of customized spare parts will undoubtedly play a pivotal role in shaping the future of production.Customized Annealing Machine Spare Parts