[Solid state HF welder with wire feed system]Exploring the Innovations of Solid State HF Welders with Wire Feed System: Revolutionizing the Welding Industry for Enhanced Efficiency and Precision
****
In the world of industrial manufacturing and metal fabrication, the demand for efficient, precise, and reliable welding solutions has never been greater. One of the most revolutionary advancements in this field is the introduction of solid-state high-frequency (HF) welders equipped with wire feed systems. This technology not only enhances the accuracy and consistency of welds but also significantly improves productivity and operational efficiency. In this article, we will explore the mechanics behind solid-state HF welders, the function of wire feed systems, and their advantages over traditional welding methods.
**Understanding Solid State HF Welders**
Solid-state HF welders utilize advanced semiconductor technology to generate high-frequency electrical currents. Unlike conventional welders that rely on bulky transformers and vacuum tube technologies, solid-state systems are compact, highly efficient, and capable of delivering precise energy outputs. These welders are designed for various metal joining applications, most notably in industries like automotive, aerospace, and metal fabrication, where the integrity of welds is crucial.
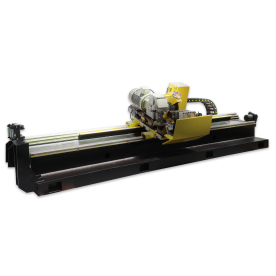
Exploring the Innovations of Solid State HF Welders with Wire Feed System: Revolutionizing the Welding Industry for Enhanced Efficiency and Precision
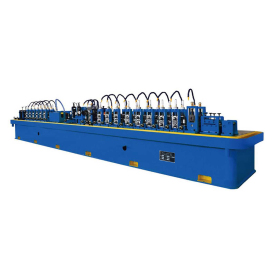
Exploring the Innovations of Solid State HF Welders with Wire Feed System: Revolutionizing the Welding Industry for Enhanced Efficiency and Precision
The core principle of solid-state HF welding is the creation of high-frequency electromagnetic fields that are used to heat and fuse materials. When metal components are placed in proximity to the electromagnetic field generated by the welder, the heat produced allows for effective bonding without melting the entire workpiece. This process minimizes distortion and helps maintain the original properties of the metals being joined, making it ideal for sensitive applications.
**The Role of Wire Feed Systems**
Wire feed systems are integral to the functionality of solid-state HF welders. These systems ensure a continuous, uniform supply of filler material during the welding process. By delivering the wire feed at a consistent rate, operators can achieve a more even distribution of heat and minimize material wastage. This continuous supply allows for a more controlled welding environment, which contributes to overall weld quality.
Typically, wire feed systems are designed to work in conjunction with solid-state HF welders, utilizing a spool of filler metal, either solid or alloyed, to enhance the bonding capability of the weld. Operators can adjust the wire feed speed based on the requirements of the specific application, enabling greater versatility and adaptability in welding projects.
**Advantages of Solid State HF Welders with Wire Feed Systems**
The combination of solid-state HF welding technology with advanced wire feed systems offers several compelling advantages:
1. **Improved Precision and Control**: The precise control over energy input and wire feed rate enables welders to achieve highly accurate and consistent welds, ensuring a better fit and finish.

Exploring the Innovations of Solid State HF Welders with Wire Feed System: Revolutionizing the Welding Industry for Enhanced Efficiency and Precision
2. **Enhanced Productivity**: The continuous feed of wire combined with rapid heating capabilities allows for faster welding speeds compared to traditional methods. This efficiency leads to higher output rates, making operations more productive overall.
3. **Reduced Heat-Affected Zone**: Since solid-state HF welding generates heat primarily at the surface of the materials being joined, the heat-affected zone (HAZ) is significantly reduced. This factor is crucial in applications that require minimal alteration of the base metal properties, such as in the manufacture of thin-walled tubes and sensitive electronic components.
4. **Lower Smoke and Fume Emissions**: In comparison to traditional welding methods, solid-state HF welders produce fewer fumes and pollutants due to the efficient heating process. This advantage translates into a cleaner working environment and contributes to better occupational safety.
5. **Cost Efficiency**: Over time, the operational efficiency and reduced material wastage offered by solid-state HF welders with wire feed systems can lead to considerable cost savings for manufacturers. The reliability and longevity of solid-state systems also contribute to lower maintenance costs.
**Conclusion**
Solid-state HF welders with wire feed systems represent a significant leap forward in welding technology. As industries demand higher quality, more efficient, and environmentally friendly welding solutions, these advanced systems fulfill that need while addressing many limitations associated with traditional welding processes. Manufacturers who embrace this innovative technology are well-positioned to enhance their production capabilities, reduce costs, and maintain a competitive edge in the ever-evolving landscape of metal fabrication. As the demand for high-quality welds continues to grow, the role of solid-state HF welders is expected to become increasingly pivotal in shaping the future of industrial welding.Heavy-Duty Cold Cutting Saw Machine