[Roller for tube mill]The Essential Role of Roller Systems in Optimizing Tube Mill Performance and Productivity: A Comprehensive Overview
****
In the realm of metalworking and manufacturing, tube mills play a crucial role in producing various tubular products used in industries ranging from construction to automotive. Among the various components that contribute to the efficiency and effectiveness of tube mills, roller systems stand out as essential elements that impact the overall performance and productivity of the mills. Understanding the significance of roller systems is paramount for manufacturers aiming to enhance production quality and operational efficiency.
Understanding Tube Mills
A tube mill is a type of industrial equipment designed to manufacture tubes by bending and welding flat strips. The process typically involves feeding raw materials into the mill where they undergo multiple stages of shaping, forming, and welding to produce different types of tubes. These tubes can vary in size, thickness, and material depending on their intended application.
The Function of Roller Systems
At the core of the tube mill are the roller systems, which play a vital role in shaping and forming the metal strips. These rollers are strategically positioned throughout the mill and serve multiple purposes, including guiding the material through the various stages of processing, applying pressure to shape the metal, and ensuring precision in the dimensions of the final product.
Rollers are typically made from high-quality materials designed to withstand immense pressure and wear during the tube-manufacturing process. Common materials include hardened steel and various alloys, which offer both durability and strength. These rollers are often engineered with specific profiles, allowing for intricate shaping and consistent results, regardless of the thickness or type of the material being processed.
Types of Rollers in Tube Mills
Different types of rollers are used in tube mills, each tailored for specific functions.
1. **Forming Rollers:** These rollers are responsible for the initial shaping of the metal strip. They typically have grooves or channels that match the desired cross-sectional shape of the tube, guiding the metal as it is bent into shape.
2. **Welding Rollers:** After the metal is formed, welding rollers come into play. These rollers hold the edges of the strip in alignment and ensure a tight fit for welding. They help create a strong seam that is vital for maintaining the structural integrity of the tube.
3. **Sizing Rollers:** These rollers ensure that the finished tube meets precise dimensional standards. They work on the completed tube to adjust its diameter and ensure that it is uniform throughout its length.
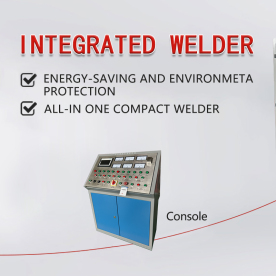
The Essential Role of Roller Systems in Optimizing Tube Mill Performance and Productivity: A Comprehensive Overview
4. **Support Rollers:** Throughout the process, support rollers help stabilize the material, preventing any deformation or misalignment as it passes through the mill.
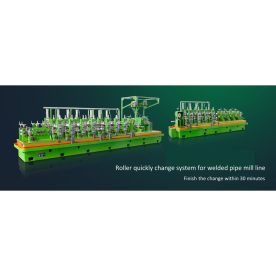
The Essential Role of Roller Systems in Optimizing Tube Mill Performance and Productivity: A Comprehensive Overview
Impact of Roller Design on Performance
The design and quality of the roller systems can significantly impact the performance of the tube mill. A well-engineered roller can enhance operational efficiency, reduce waste, and lower the chances of material defects.
1. **Material Consistency:** With high-quality rollers, manufacturers can achieve better material consistency, leading to fewer defects and rejections. Uniform rollers contribute to maintaining the same pressure levels across the product, ensuring a more uniform final output.
2. **Cost Efficiency:** The longevity and durability of rollers directly affect maintenance costs. High-quality rollers that are resistant to wear and tear can lead to reduced downtime and lower operational costs.
3. **Flexibility and Versatility:** Modern roller designs allow manufacturers to switch between different product profiles more seamlessly. This flexibility is increasingly vital in today’s market, where demand for varied products can fluctuate rapidly.
Maintenance of Roller Systems
To ensure the optimal performance of roller systems in tube mills, regular maintenance is crucial. This includes routine inspections, lubrication, and alignment checks. Preventative maintenance helps in identifying potential issues early, thereby reducing the risk of breakdowns and ensuring long-term performance of the rollers.
Conclusion
In summary, roller systems are integral to the efficient operation of tube mills. From forming to sizing, these components play a pivotal role in ensuring that the final product meets strict quality standards. By investing in high-quality roller systems and maintaining them proactively, manufacturers can enhance productivity, reduce costs, and ultimately achieve greater success in their operations. As the industry continues to evolve, the importance of advanced roller technologies will only increase, making them a central focus for manufacturers aiming to stay competitive in the market.

The Essential Role of Roller Systems in Optimizing Tube Mill Performance and Productivity: A Comprehensive Overview
By recognizing the essential role of roller systems in tube mills, manufacturers can prioritize innovations that drive efficiency and improve the quality of their products, securing their place in a competitive landscape.High-efficiency pipe mill production line