[Pipe mill production line with welding and cutting functions]Maximizing Efficiency and Quality: Innovations in Pipe Mill Production Line with Welding and Cutting Functions
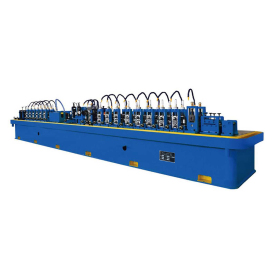
Maximizing Efficiency and Quality: Innovations in Pipe Mill Production Line with Welding and Cutting Functions
The modern pipe mill production line has revolutionized the manufacturing of pipes, catering to a variety of industries including construction, oil and gas, and infrastructure development. Central to this advancement are the integrated welding and cutting functions, which not only enhance the efficiency of the production process but also significantly improve the quality of the final product. In an era where precision and speed are paramount, the evolution of these functions has become a focal point for manufacturers striving to meet the rigorous demands of the market.
**Understanding the Pipe Mill Production Line**
At its core, a pipe mill production line is designed to transform raw materials, usually in the form of steel coils or strips, into finished pipes through a series of processes. These include forming, welding, and cutting—all of which play crucial roles in determining the quality and functionality of the pipes. The incorporation of advanced welding and cutting technologies in these lines streamlines production, reduces waste, and ensures that the pipes meet necessary specifications and standards.
**The Significance of Welding in Pipe Production**
Welding is perhaps the most critical function within the production line. It is the process that joins the edges of the formed strip to create a hollow pipe. Modern pipe mills utilize various welding techniques, with the most common beingElectric Resistance Welding (ERW) and Submerged Arc Welding (SAW). ERW has gained popularity for its speed and efficiency, using electricity to heat the edges of the steel strip until they melt and bond together. On the other hand, SAW is preferred for producing larger diameter pipes and thicker wall thicknesses, as it uses a continuous electrode to deliver heat and filler metal, ensuring a robust weld.
The integration of automation in welding processes has further improved quality control. Automated welding systems are equipped with advanced cameras and sensors, which continuously monitor the quality of the welds in real-time. This data-driven approach allows manufacturers to address any issues instantly, reducing the risk of defects and ensuring consistency across batches.
**Cutting Functions and Their Importance**
After the welding process, the next critical function is cutting. The cut length of the final product can be customized depending on customer specifications, and this flexibility is vital in meeting varying market needs. Automated cutting systems, often utilizing plasma or laser cutting technologies, provide precise and clean cuts that minimize post-processing work. These methods not only enhance accuracy but also increase the speed of production, allowing manufacturers to cater to high-demand situations without compromising quality.
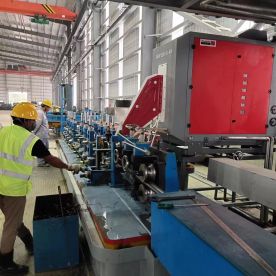
Maximizing Efficiency and Quality: Innovations in Pipe Mill Production Line with Welding and Cutting Functions
Moreover, advanced cutting systems often incorporate software that allows manufacturers to optimize their production schedules and material usage. This intelligence reduces waste and ensures that the maximum quality is extracted from the raw materials, leading to increased profitability.
**Integration and Automation: A Game Changer**
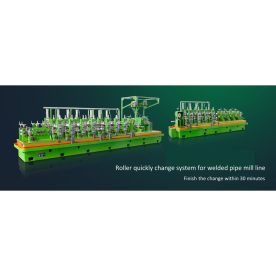
Maximizing Efficiency and Quality: Innovations in Pipe Mill Production Line with Welding and Cutting Functions
The true power of a pipe mill production line with welding and cutting functions lies in its integration. Manufacturers are increasingly adopting fully automated systems that unite welding, cutting, and other functions into a seamless workflow. Such integration not only increases operational efficiency but also reduces the likelihood of human error. With less manual intervention, production lines can run continuously and reliably, meeting large-scale demand with ease.
Additionally, modern production lines come equipped with advanced software solutions that handle everything from inventory management to quality assurance. These technologies allow manufacturers to gather insights into their operations, facilitating continuous improvement in processes.
**Conclusion**
In summary, the incorporation of welding and cutting functions in modern pipe mill production lines is a testament to the advancements in manufacturing technology. These functions not only play a critical role in enhancing the efficiency and quality of pipe production but also provide manufacturers the agility to respond to a dynamic market. By leveraging automation and integrated systems, businesses can maximize productivity, minimize waste, and optimize the overall production process, paving the way for continued growth and innovation in the industry. As manufacturing demands evolve, the importance of a robust, efficient pipe mill production line cannot be overstated—it is pivotal for delivering high-quality products that meet the needs of today’s fast-paced industrial landscape.Tube mill production line