[All-in-one High Frequency Welder for Metal Processing]Revolutionizing Metal Manufacturing: The Advantages of the All-in-One High Frequency Welder for Metal Processing Industry
****
The metal processing industry has witnessed significant advancements in technology over the past few decades, leading to increased efficiency, improved quality, and better ergonomic practices. A standout innovation in this sector is the All-in-One High Frequency Welder, which integrates several functions designed specifically for metal processing applications. This article explores the multifaceted benefits of this sophisticated equipment, shedding light on why it has become indispensable in modern manufacturing environments.
What is an All-in-One High Frequency Welder?
The All-in-One High Frequency Welder combines the capabilities of standard welding machines with additional features that enhance productivity and versatility. Unlike traditional welding methods that typically require separate machines for different processes, this innovative system enables seamless transitions between tasks. It employs high-frequency electrical currents to create heat and fuse metal surfaces, making it ideal for a variety of applications ranging from sheet metal fabrication to heavier structural components.
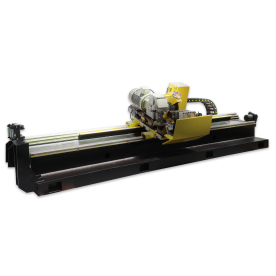
Revolutionizing Metal Manufacturing: The Advantages of the All-in-One High Frequency Welder for Metal Processing Industry
Versatility Across Applications
One of the leading advantages of an All-in-One High Frequency Welder is its versatility. This equipment is designed to work with multiple types of metals including steel, aluminum, copper, and other alloys. This adaptability allows manufacturers to use the same machine for diverse projects, which reduces downtime and minimizes the need for multiple specialized welders. As industries shift toward lean production techniques, this enhancement has become increasingly critical.
Improved Efficiency and Productivity
The efficiency of the All-in-One High Frequency Welder is unmatched. Traditional welding methods can be time-consuming, often requiring preheating and extensive post-processing. The high-frequency approach accelerates this process, producing strong and reliable welds in a fraction of the time. Welders equipped with high-frequency technology also tend to consume less energy, which is not only cost-effective but also aligns with global sustainability efforts.
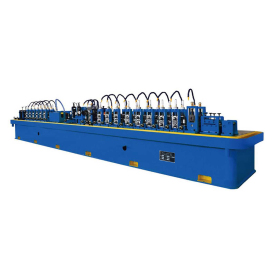
Revolutionizing Metal Manufacturing: The Advantages of the All-in-One High Frequency Welder for Metal Processing Industry
Additionally, the automated features present in many of these welders eliminate repetitive manual tasks. Automation reduces the likelihood of human error, enhances accuracy, and allows operators to focus on more complex activities. By integrating intelligent control systems, the All-in-One High Frequency Welder can adjust parameters automatically, optimizing the weld quality based on the specific characteristics of the materials being joined.
Enhanced Weld Quality
In the realm of metallurgy, weld quality is paramount. The high-frequency welding technique produces exceptionally strong welds with minimal distortion. The fine control over heating and cooling gradients reduces the risk of structural weakness, ensuring that the final product meets or exceeds the necessary quality standards. Furthermore, this method minimizes the formation of imperfections, leading to a cleaner finish which is essential for aesthetic applications.
The ability to achieve consistent and high-quality results across various projects is crucial for businesses aiming to enhance their reputation and customer satisfaction. The reliability of weld quality in an All-in-One High Frequency Welder signifies a noteworthy benefit for companies looking to maintain competitive advantages.
User-Friendly Design and Ergonomics
The design of modern All-in-One High Frequency Welders prioritizes user-friendliness and ergonomics. Many devices include touchscreen interfaces that simplify programming and operation. These intuitive controls enable operators to make quick adjustments, view real-time data, and monitor the welding process efficiently. Additionally, lightweight materials and compact designs make these machines easier to transport, set up, and operate within the workspace, reducing the physical strain on the user.
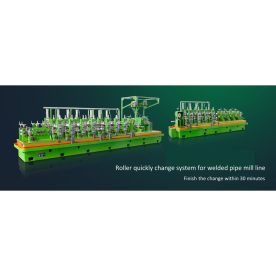
Revolutionizing Metal Manufacturing: The Advantages of the All-in-One High Frequency Welder for Metal Processing Industry
Economic Impact and Return on Investment
The initial investment in an All-in-One High Frequency Welder can be significant; however, the long-term economic benefits are compelling. Reduced labor costs due to automation, minimized energy consumption, and lower maintenance requirements contribute to an attractive return on investment. The ability to complete projects faster while maintaining high quality also drives revenue growth, providing manufacturing businesses with the leverage they need to thrive in a competitive environment.
Conclusion
Embracing advanced technology such as the All-in-One High Frequency Welder for metal processing can significantly transform manufacturing practices. From enhanced productivity and improved weld quality to user-friendly designs and economic efficiency, this innovative equipment stands at the forefront of the industry’s evolution. As manufacturers continue to seek solutions that meet changing demands, the All-in-One High Frequency Welder is an invaluable asset poised to empower the future of metal processing.Spare Parts Kit for Solid State HF Welders