[Tube making machine for industrial applications]Exploring the Innovations and Industrial Applications of Tube Making Machines: A Comprehensive Guide for Modern Manufacturing
****
In the realm of industrial manufacturing, tube making machines play a pivotal role in producing a wide range of products used across various sectors. From automotive and aerospace to construction and medical industries, these machines are essential for creating tubes that meet specific dimensional, material, and quality standards. As technology advances, tube making machines have evolved to incorporate cutting-edge features, ensuring efficiency, precision, and adaptability. This article delves into the workings of tube making machines, their applications, benefits, and the future prospects of this integral machinery.
Understanding Tube Making Machines
A tube making machine is designed to shape and manufacture tubes from raw materials, typically metal, plastic, or composite materials. These machines utilize a combination of forming, welding, and finishing processes to create tubes that can be used for multiple purposes, such as structural support, fluid transfer, and containment. The primary functions of tube making machines can be summarized as follows:
1. **Forming**: The initial stage involves feeding raw material into the machine, where it is shaped into a tubular form. This can be accomplished through various methods, including roll forming, extrusion, and bending.
2. **Welding**: Many tubes require welding to secure their structural integrity. Tube making machines often integrate welding techniques that include high-frequency induction welding, laser welding, or TIG welding. This step is critical for achieving high strength and durability.
3. **Cutting and Finishing**: Once the tube is formed and welded, it is cut to the desired length and subjected to finishing processes. These processes may include cleaning, deburring, and surface treatment to enhance quality and performance.
Industrial Applications of Tube Making Machines
The applications of tube making machines span several industries, reflecting their versatility. Here are some of the significant sectors that rely on tube making technology:
**1. Automotive Industry**
The automotive sector is one of the largest consumers of tubing products. Tube making machines are used to produce exhaust pipes, fuel lines, and structural components, ensuring that vehicles meet safety and performance standards. With increasing focus on lightweight materials, manufacturers are turning to advanced tube making techniques using high-strength steel and aluminum alloys.
**2. Aerospace Sector**
In aerospace, tube making machines are critical for crafting components that withstand high stress and temperature. Aerospace applications often require tubes for fuel systems, hydraulic lines, and structural elements. The manufacturing process must adhere to rigorous safety standards and precision engineering to ensure reliability in flight operations.
**3. Construction Industry**
Tubes are fundamental in the construction industry, where they are used for scaffolding, support structures, and plumbing systems. Tube making machines facilitate the production of strong, durable tubes that can withstand environmental stresses. The ability to customize tube dimensions and properties allows builders to meet specific project requirements.
**4. Medical Applications**
The medical field demands precision-engineered tubes for various applications, including medical devices, implantable structures, and fluid delivery systems. Tube making machines that specialize in producing biocompatible and sterile tubes are essential in this sector, ensuring patient safety and compliance with health regulations.
**5. Oil and Gas Industry**
The oil and gas sector relies heavily on tube making machines for creating pipelines, drilling equipment, and other infrastructure components. These tubes must be robust enough to endure harsh environmental conditions and high-pressure applications.
Advantages of Using Tube Making Machines
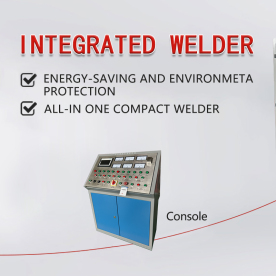
Exploring the Innovations and Industrial Applications of Tube Making Machines: A Comprehensive Guide for Modern Manufacturing
Investing in tube making machines provides numerous benefits for manufacturers, including:
– **Efficiency**: Modern tube making machines operate at high speeds, significantly reducing production time and labor costs. Automated systems can handle multiple operations simultaneously, further enhancing throughput.
– **Quality Control**: Advanced technologies, including real-time monitoring and quality inspection systems, ensure that the tubes produced meet stringent standards. This capability results in fewer defects and higher customer satisfaction.
– **Customization**: Manufacturers can tailor tube dimensions, materials, and finishes to meet specific customer requirements. This flexibility allows for the production of specialized products that cater to niche markets.
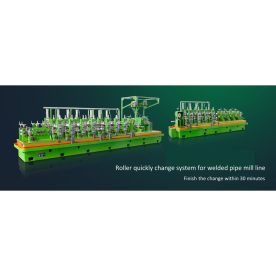
Exploring the Innovations and Industrial Applications of Tube Making Machines: A Comprehensive Guide for Modern Manufacturing
– **Cost-Effectiveness**: By optimizing production processes and minimizing waste, tube making machines can lower manufacturing costs. This advantage makes it easier for companies to compete in a dynamic market.

Exploring the Innovations and Industrial Applications of Tube Making Machines: A Comprehensive Guide for Modern Manufacturing
The Future of Tube Making Machines
As industries evolve, tube making machines are likely to see further advancements in automation, material science, and energy efficiency. The rising demand for sustainable manufacturing practices may also drive innovations in tube design, leading to lighter and more environmentally friendly products.
In conclusion, tube making machines are an indispensable asset in modern industrial applications. Their ability to produce high-quality tubes efficiently across diverse sectors underscores their significance in the manufacturing landscape. As technological advancements continue, the future of tube making holds great promise for manufacturers looking to enhance their production capabilities.All-in-one High Frequency Welder with Adjustable Power