[ERW tube mill]Understanding the Importance and Functionality of ERW Tube Mill in Modern Manufacturing Processes
**Introduction**
In today’s rapidly evolving manufacturing landscape, the demand for high-quality and precision-engineered products has never been more critical. One essential piece of equipment that plays a vital role in producing various metal components is the Electric Resistance Welded (ERW) tube mill. This innovative machine enables manufacturers to create welded tubes efficiently, contributing to a spectrum of industries such as construction, automotive, and energy production. In this article, we will delve into the intricacies of the ERW tube mill, its operations, advantages, and applications, highlighting its importance in modern manufacturing processes.
**What is an ERW Tube Mill?**
An ERW tube mill is a sophisticated piece of machinery designed explicitly for manufacturing welded steel tubes and pipes. Unlike traditional methods that may utilize different welding techniques, the ERW tube mill employs electric resistance welding to join the edges of steel strips or plates. This process involves passing electric current through the steel, generating heat due to resistance, and ultimately fusing the materials.
The key components of an ERW tube mill include:
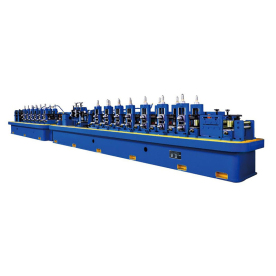
Understanding the Importance and Functionality of ERW Tube Mill in Modern Manufacturing Processes
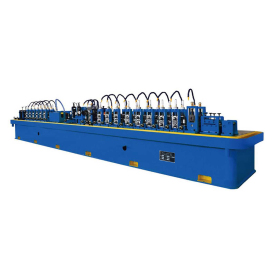
Understanding the Importance and Functionality of ERW Tube Mill in Modern Manufacturing Processes
1. **Uncoiler**: This is where the raw steel coil is unwound and prepared for processing. 2. **Rollers**: The mill utilizes a series of rollers to shape the flat steel strip into a tubular form. 3. **Welding Station**: Here, the edges of the tube are welded together using electric resistance. 4. **Sizing Section**: This is where the diameter of the tube is precisely controlled and adjusted. 5. **Cooling System**: After welding, the tube passes through a cooling system to ensure it maintains its structural integrity. 6. **Cut-off Section**: Finally, the tubes are cut to the desired lengths for shipment or further processing.
**How ERW Tube Mills Operate**
The operation of an ERW tube mill starts with feeding a flat steel strip into the machine. The strip is first unwound from a coil and then progressively shaped into a cylindrical form through a series of rollers. As the edges meet, they are welded together using an electric current that heats the steel until it reaches the melting point, effectively creating a strong seam.
After the welding process, the newly formed tube goes through several stages, including sizing and cooling. The sizing process ensures that the tube meets precise specifications and tolerances, which is critical in applications where fit and function are paramount. Once sized, the tube is cooled to eliminate any stresses introduced during the welding phase.
**Advantages of Using ERW Tube Mills**
1. **Efficiency**: ERW tube mills are known for their high production speeds, significantly reducing manufacturing time when compared to traditional welding methods. This efficiency is particularly beneficial in large-scale production environments.
2. **Cost-Effective**: The process of electric resistance welding is not only faster but also more cost-effective, producing less waste material and requiring less energy than other welding techniques.
3. **High Strength and Quality**: The welded joints produced by ERW tube mills are remarkably strong and possess consistent quality. This reliability is essential for applications in the automotive and aerospace industries where safety is a major concern.
4. **Versatility**: ERW tube mills can be used to manufacture tubes of varying sizes and shapes, including round, square, and rectangular profiles. This versatility allows manufacturers to cater to a diverse array of customer needs.
5. **Environmentally Friendly**: Modern ERW tube mills are designed with energy-efficient technologies that help reduce the carbon footprint of the manufacturing process. This aspect is increasingly important as industries aim to adopt more sustainable practices.
**Applications of ERW Tubes**
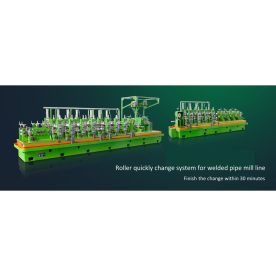
Understanding the Importance and Functionality of ERW Tube Mill in Modern Manufacturing Processes
ERW tubes have a broad range of applications across several industries:
– **Construction**: Used in structural applications, scaffolding, and support frameworks due to their strength and reliability. – **Automotive**: Critical in the manufacturing of exhaust systems, roll bars, and other automotive structures where durability is key. – **Energy**: Employed in various energy sectors, including oil and gas pipelines and renewable energy structures. – **Transportation**: Commonly utilized in the manufacturing of railings and support systems for public transport infrastructures.
**Conclusion**
The ERW tube mill represents a significant advancement in tube manufacturing technology, enabling industries to produce high-quality welded tubes efficiently and economically. With its numerous advantages, from speed and cost-effectiveness to versatility and strength, the ERW tube mill is an indispensable tool in modern manufacturing. As industries continue to evolve and adapt to new challenges, the role of ERW tube mills will undoubtedly remain crucial in meeting the demands of the future.Induction heating equipment