[High-precision tube making machine ]Revolutionizing Manufacturing with High-Precision Tube Making Machines: A Comprehensive Guide to Their Benefits and Applications
In the world of manufacturing, precision and efficiency are paramount. As industries evolve and demand for high-quality products increases, the need for advanced manufacturing technologies also rises. One such innovation that has significantly transformed various sectors is the high-precision tube making machine. This cutting-edge equipment is engineered to produce tubes with remarkable accuracy and consistency, catering to a diverse range of applications from automotive to aerospace.
At its core, the high-precision tube making machine is designed to fabricate tubes with exact dimensions, which is critical for industries that require stringent tolerances. These machines utilize advanced technologies such as computer numerical control (CNC), which allows for automated operation and the ability to manage complex shapes and profiles. This level of control minimizes human error, improves production speed, and enhances overall output quality.
One of the primary advantages of high-precision tube making machines is their ability to produce tubes with varying wall thicknesses and diameters while maintaining precision. This flexibility is crucial for manufacturers that require custom solutions for specific projects. Whether it involves producing thin-walled tubes for intricate applications or thicker tubes that need to withstand high pressure and temperature, modern machines can cater to these requirements efficiently.
The industries that benefit from high-precision tube making machines are numerous. In the automotive sector, for instance, the demand for lightweight yet robust components is ever-growing. High-precision tubes are essential in manufacturing fuel lines, exhaust systems, and chassis components. These tubes not only contribute to improved performance and fuel efficiency but also enhance the safety and reliability of vehicles.
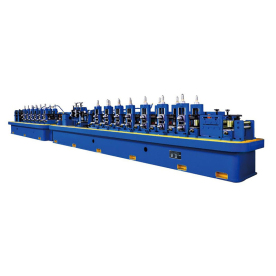
Revolutionizing Manufacturing with High-Precision Tube Making Machines: A Comprehensive Guide to Their Benefits and Applications
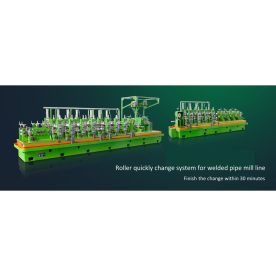
Revolutionizing Manufacturing with High-Precision Tube Making Machines: A Comprehensive Guide to Their Benefits and Applications
Similarly, in the aerospace industry, the need for high-quality tubes cannot be overstated. Components used in aircraft must undergo rigorous testing to ensure they can withstand extreme conditions. Here, high-precision tube making machines come into play by producing lightweight, durable tubes that meet strict regulatory standards. The aerospace industry’s reliance on these machines has grown, as manufacturers strive to enhance aircraft performance, reduce emissions, and improve overall passenger safety.
Beyond the automotive and aerospace sectors, high-precision tube making machines are also vital in medical devices manufacturing. In this industry, precision is critical due to the specifications required for various instruments such as catheters, stents, and syringes. Medical devices must be manufactured to exacting standards to ensure patient safety and device efficacy. As a result, high-precision tube making machines have become essential tools, allowing manufacturers to create components that meet both regulatory standards and patient needs.
Moreover, the global push for sustainability and eco-friendliness has also led to innovations in tube making machinery. Many modern high-precision machines are designed to optimize material usage, reducing waste and conserving resources during the manufacturing process. This is not only beneficial for the environment but can also lead to significant cost savings for manufacturers. By improving efficiency and reducing unnecessary waste, companies can operate more sustainably while boosting their bottom line.
Furthermore, high-precision tube making machines are increasingly equipped with smart technology. These machines can be integrated into Industry 4.0 environments, enabling manufacturers to monitor processes in real-time, collect data, and conduct predictive maintenance. This level of connectivity enhances efficiency and allows for quick identification of potential issues before they escalate into costly downtime.

Revolutionizing Manufacturing with High-Precision Tube Making Machines: A Comprehensive Guide to Their Benefits and Applications
In conclusion, high-precision tube making machines are revolutionizing the way industries approach manufacturing. Their ability to produce tubes with exact specifications fundamentally improves product quality, enhances safety, and fulfills the unique requirements of various sectors. As technology continues to advance, these machines will likely play an even more significant role in the evolution of manufacturing processes, ensuring increased efficiency, sustainability, and innovation across the board. For manufacturers looking to gain a competitive edge, investing in high-precision tube making technology is a strategic move that promises substantial long-term benefits.Precision-control All-in-one Welding Equipment