[Customized ERW tube mill solutions]Innovative and Customized ERW Tube Mill Solutions: Meeting Industry Demands for Efficient and High-Quality Steel Pipes and Tubes
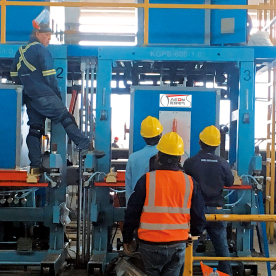
Innovative and Customized ERW Tube Mill Solutions: Meeting Industry Demands for Efficient and High-Quality Steel Pipes and Tubes
In the ever-evolving landscape of industrial manufacturing, the demand for high-quality steel pipes and tubes continues to surge. This rise is fueled by applications across diverse sectors, including construction, automotive, and energy. As a result, organizations are increasingly turning to Customized ERW (Electric Resistance Welded) tube mill solutions to optimize production processes, enhance product quality, and meet specific market requirements. This article explores the features and benefits of tailored ERW tube mills, as well as how they can significantly impact manufacturing efficiency and product integrity.
Understanding ERW Tube Mills
ERW tube mills are specialized equipment used to produce welded steel pipes and tubes from coiled or flat sheet metal. The process involves the continuous formation of a strip into a circular shape, followed by the welding of the edges using electric resistance. The unique welds created through this method ensure strong and durable tubes, which can be further processed for various applications.
For manufacturers, having a reliable and efficient tube mill is crucial. However, the one-size-fits-all model often does not cater to the diverse needs of different industries. Customization addresses this gap by allowing manufacturers to modify the equipment and processes based on specific requirements.
The Importance of Customization
Customization in ERW tube mills is pivotal for several reasons:
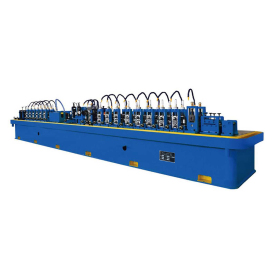
Innovative and Customized ERW Tube Mill Solutions: Meeting Industry Demands for Efficient and High-Quality Steel Pipes and Tubes
1. **Adaptability to Market Trends**: Industries often face rapid changes in demand driven by factors such as technological advancements and changing consumer preferences. Customized ERW tube mills can be adjusted quickly to produce different dimensions, shapes, and grades of steel tubes, enabling manufacturers to adapt and stay competitive.
2. **Optimization of Production Processes**: Customized solutions allow for the integration of advanced technologies such as automation and real-time monitoring systems. These enhancements lead to immediate feedback during production, reducing waste, minimizing errors, and maximizing throughput. As a result, manufacturers can significantly decrease operational costs while increasing output.
3. **Enhanced Quality Control**: The ability to tailor an ERW tube mill means manufacturers can implement specific quality control measures suited to their production standards. Increased process control leads to improved consistency in weld quality, mechanical properties, and surface finish of the tubes, ensuring the end products meet rigorous industry standards.
4. **Increased Safety**: Custom solutions can also incorporate safety features that align with the specific operational environment. This can include advanced protection systems, employee training modules tailored to the machinery, and ergonomics enhancements that ensure a safer workplace.
5. **Sustainability**: As global focus on sustainability increases, so does the pressure on the manufacturing sector to adopt environmentally-friendly practices. Customized ERW tube mills can be designed to minimize energy consumption and waste generation, resulting in a smaller ecological footprint while complying with stricter regulations.
Key Features of Customized ERW Tube Mill Solutions
When investing in customized ERW tube mills, manufacturers can consider several key features that can be tailored:
– **Material Handling Systems**: Customized solutions can facilitate efficient feeding, transport, and storage of raw materials, ensuring smooth workflow and reducing downtime. – **Welding Technology**: The welding process can be fine-tuned to meet specific material types and thicknesses. This includes options for high-frequency welding and laser technologies which enhance weld quality and speed.
– **Flexible Sizing Options**: Custom mills can be adapted to produce a wide range of tube sizes, from small-diameter tubes for specialty applications to heavy-duty tubes used in oil and gas pipelines.
– **Post-Processing Capabilities**: Options for additional processing such as cutting, straightening, and surface finishing can be integrated directly into the tube mill, resulting in a streamlined operation from start to finish.
Conclusion

Innovative and Customized ERW Tube Mill Solutions: Meeting Industry Demands for Efficient and High-Quality Steel Pipes and Tubes
In conclusion, investing in Customized ERW tube mill solutions provides manufacturers, across various industries, with the agility they require to thrive in a competitive market. The advantages of enhanced adaptability, optimized production processes, improved quality control, increased safety, and sustainability make customized solutions a smart choice. As the demand for effective, high-quality tube and pipe solutions continues to grow, embracing customization will be vital for businesses aiming to succeed in today’s dynamic industrial landscape.Tube making machine