[Customized ERW tube mill solutions]Innovative Customized ERW Tube Mill Solutions: Optimizing Production and Efficiency for Modern Manufacturing Needs
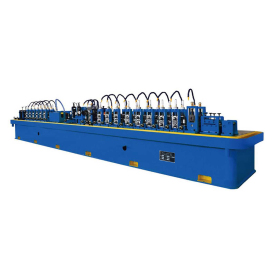
Innovative Customized ERW Tube Mill Solutions: Optimizing Production and Efficiency for Modern Manufacturing Needs
In the world of manufacturing, precision and efficiency are paramount. As industries evolve, the demand for specialized production solutions has grown significantly. One such innovation is the Customized Electric Resistance Welded (ERW) tube mill solutions, which cater to diverse applications across various sectors. By integrating advanced technology and bespoke engineering, these custom-designed tube mills offer manufacturers unparalleled flexibility and performance in producing welded tubes.
Understanding ERW Tube Mills
Electric Resistance Welding (ERW) is a process that joins two pieces of metal together using heat generated by electrical resistance. The method is commonly employed in creating tubular products for industries, including automotive, construction, and oil & gas. ERW tube mills utilize advanced machinery to produce a range of tube sizes and shapes, often enhancing productivity and lowering production costs.
The Need for Customized Solutions
Every manufacturer has unique requirements based on their product specifications, scale, and operational workflow. Standard tube mill solutions may not meet specific needs, leading to inefficiencies, waste, and higher operational costs. This is where customized ERW tube mill solutions come into play. These tailor-made systems are designed to align with a manufacturer’s objectives, whether it be improving speed, enhancing precision, or lowering overall production costs.
Key Benefits of Customized ERW Tube Mill Solutions
1. **Tailored Configuration**: Customized ERW tube mills allow for the design of machinery that fits perfectly within the manufacturer’s operations. This includes bespoke adjustments in terms of tube size, wall thickness, and material type. By purchasing a mill designed for their needs, manufacturers can optimize their processes and reduce downtime.
2. **Enhanced Productivity**: With the right design and specifications, customized ERW tube mills can significantly boost production rates. Automation features and advanced control systems can be incorporated, allowing for continuous operation with minimal interruption. This increase in efficiency translates into higher output and quicker turnaround times for orders.
3. **Cost Efficiency**: While the initial investment in a customized ERW tube mill may be higher than standard equipment, the long-term savings make it worthwhile. Reduced material waste, lower energy consumption, and fewer labor costs can result in significant savings. Additionally, the durability and reliability of custom solutions often lead to reduced maintenance costs over time.
4. **Improved Quality Control**: Customized solutions can incorporate specific quality control measures tailored to a manufacturer’s needs. This ensures that each tube produced adheres to stringent quality standards, with minimal defects. Enhanced quality control can lead to better customer satisfaction and fewer returns, further boosting a company’s reputation.
5. **Scalability**: As businesses grow and evolve, their production needs can change dramatically. Customized ERW tube mills can be designed with scalability in mind, allowing for upgrades and expansions without needing to replace entire systems. This flexibility ensures that manufacturers are always equipped to respond to shifting market demands.
Industry Applications
Custom ERW tube mills find applications in various sectors, including:
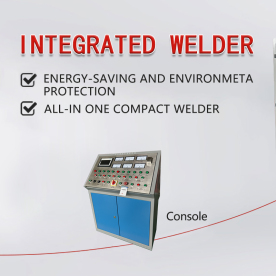
Innovative Customized ERW Tube Mill Solutions: Optimizing Production and Efficiency for Modern Manufacturing Needs
– **Automotive Manufacturing**: Tubes are essential for vehicle structures, exhaust systems, and other components. Custom solutions allow for the production of complex shapes and sizes required by automotive engineers.
– **Construction**: The construction industry relies heavily on tubular products, whether for scaffolding, framing, or piping. Customized solutions enable builders to source materials that meet specific project requirements.
– **Oil & Gas**: In this sector, the integrity of welded tubes is critical. Custom ERW tube mills can produce high-strength tubes designed to withstand the harsh environments found in drilling operations.
Conclusion
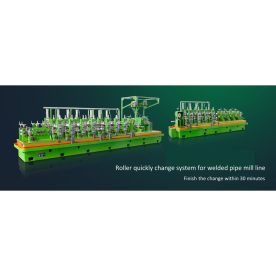
Innovative Customized ERW Tube Mill Solutions: Optimizing Production and Efficiency for Modern Manufacturing Needs
In today’s competitive manufacturing landscape, staying ahead requires innovation and adaptability. Customized ERW tube mill solutions offer a pathway for manufacturers to enhance their productivity, efficiency, and product quality. By investing in tailored machinery, businesses not only optimize their operations but also position themselves for long-term success in their respective industries. As technology continues to advance, the importance of customized solutions will only grow, ensuring that manufacturers maintain a competitive edge while meeting the ever-evolving demands of the marketplace.Energy-saving induction heating equipment