[Industrial-grade induction heating equipment]Understanding the Importance and Benefits of Industrial-Grade Induction Heating Equipment in Modern Manufacturing Processes
Induction heating has revolutionized many sectors of manufacturing, providing a reliable and efficient heating method. Among the various types of heating technologies, industrial-grade induction heating equipment stands out for its ability to deliver precise and controllable heat application. This article delves into the significance, advantages, and operational principles of industrial-grade induction heating equipment in manufacturing processes.
What is Industrial-Grade Induction Heating Equipment?
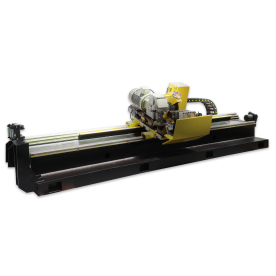
Understanding the Importance and Benefits of Industrial-Grade Induction Heating Equipment in Modern Manufacturing Processes
Induction heating is a process that uses electromagnetic induction to heat electrically conductive materials, such as metals. Industrial-grade induction heating equipment is designed for heavy-duty applications, capable of delivering high power output and temperature consistency necessary for large-scale operations.
The equipment comprises several key components: an induction coil, a high-frequency power supply, and a workpiece. The induction coil generates a magnetic field, which induces an electric current in the conductive material, resulting in rapid heating. This setup is particularly effective for processes such as forging, brazing, heating, welding, and hardening.
Advantages of Industrial-Grade Induction Heating Equipment
1. **Energy Efficiency**: One of the primary benefits of induction heating is its energy efficiency. Unlike conventional heating methods, which heat the entire workpiece and surrounding environment, induction heating focuses energy directly where it is needed. This concentrated panel of heat reduces waste and lowers operational costs.
2. **Precise Temperature Control**: Industrial-grade induction heating equipment allows for accurate temperature setting and control. This aspect is crucial in applications where specific temperatures and heating rates are required to achieve desired metallurgical properties. The feedback systems integrated into advanced equipment ensure that temperature fluctuations are minimized, leading to more consistent results.
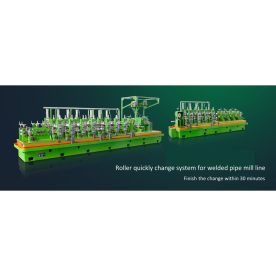
Understanding the Importance and Benefits of Industrial-Grade Induction Heating Equipment in Modern Manufacturing Processes
3. **Speed**: Induction heating processes are significantly faster compared to traditional methods. The rapid heating capabilities of industrial-grade equipment enable faster cycle times, enhancing overall productivity. For instance, materials can heat up to several hundred degrees Celsius in just seconds, reducing downtime and increasing throughput.
4. **Improved Product Quality**: The precise heating offered by induction equipment leads to improved product quality. The uniform heating minimizes the risk of warping or damage, ensuring that finished products meet strict quality standards. Moreover, the process minimizes oxidation and contamination, which can occur during prolonged heating in conventional methods.

Understanding the Importance and Benefits of Industrial-Grade Induction Heating Equipment in Modern Manufacturing Processes
5. **Safety**: Modern industrial-grade induction heating equipment is built with enhanced safety features. The absence of open flames or hot surfaces reduces the risk of accidents. Furthermore, many systems have built-in cooling mechanisms, monitoring capabilities, and emergency shut-off features, creating a safer working environment.
6. **Versatility**: Induction heating is not limited to a single application. The equipment can effectively cater to various processes such as induction hardening, tempering, soldering, and even drying or curing coatings. This versatility makes it an indispensable tool across multiple industries, including automotive, aerospace, and manufacturing.
Applications of Industrial-Grade Induction Heating Equipment
Induction heating systems are employed in various industries for different applications:
– **Metal Forging**: In metal forging, induction heating is used to preheat metals for increased malleability, leading to improved shapes and designs. – **Brazing and Soldering**: The precise application of heat enables effective brazing and soldering of components without damaging the adjoining parts, maintaining quality and integrity. – **Hardening and Annealing**: Induction heating is widely used for hardening and annealing processes, where specific material properties are achieved through controlled heating and cooling cycles.
– **Heat Shrinking**: This process employs induction heating to shrink fit components onto shafts or other fittings, ensuring a secure and tight assembly.
Conclusion
Industrial-grade induction heating equipment represents a leap forward in heating technology for manufacturing. Its numerous advantages, including energy efficiency, speed, precision, and versatility, make it an essential tool in modern production lines. As industries continue to push for advancements in technology and quality, the role of induction heating equipment is expected to expand, further solidifying its importance in manufacturing processes. Embracing this technology not only enhances operational efficiency but also contributes to cost savings and superior product quality, driving innovation in the industrial landscape.Solid state high frequency welder machine