[Custom-Made Spare Parts for Solid State HF Welders]Optimizing Performance and Efficiency with Custom-Made Spare Parts for Solid State HF Welders: The Key to Enhanced Productivity and Longevity
In the ever-evolving landscape of manufacturing and industrial applications, the role of high-frequency (HF) welders is becoming increasingly vital. Solid state HF welders, known for their precision and adaptability, represent a significant technological advancement in the welding industry. However, like any complex machinery, they require regular maintenance and occasional replacement of parts to operate at peak efficiency. This is where custom-made spare parts for solid state HF welders play a critical role, providing tailored solutions that can significantly enhance the performance, efficiency, and longevity of these essential machines.
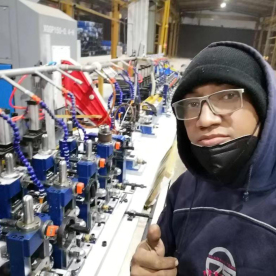
Optimizing Performance and Efficiency with Custom-Made Spare Parts for Solid State HF Welders: The Key to Enhanced Productivity and Longevity
The Importance of Custom-Made Spare Parts
One size does not fit all, especially in industrial applications where precision and reliability are paramount. Solid state HF welders are typically used for a variety of welding tasks, including but not limited to thermoplastic welding, metal joining, and packaging applications. The diverse nature of these applications means that the wear and tear on components can vary widely based on usage and environmental factors. Custom-made spare parts ensure that every piece can be specifically designed to meet the unique demands of a particular welding application, which is crucial for maintaining high quality and consistency in production.
Moreover, custom parts often enhance operational efficiency. Off-the-shelf components may not fit perfectly or may not match the exact specifications needed for optimal performance. This can lead to increased downtime, frequent replacements, and ultimately higher maintenance costs. In contrast, custom-made spare parts are designed to work seamlessly with existing systems, minimizing the risk of operational disruptions and improving overall productivity.
Advantages of Using Custom-Made Spare Parts
1. **Perfect Fit and Compatibility**: Custom-made spare parts are designed to fit seamlessly into the specific solid state HF welding machines. This reduces the risk of misalignment, minimizing the chances of mechanical failures that can occur with ill-fitting components.
2. **Enhanced Performance**: Custom components can be engineered to offer superior performance characteristics. This includes improved thermal conductivity, better energy efficiency, and enhanced durability under extreme working conditions.
3. **Cost-Effectiveness**: While the initial investment in custom parts may be higher than standard alternatives, the long-term savings associated with reduced breakdowns and less downtime make them a wise financial choice. Businesses can also experience fewer production interruptions, which translates to higher outputs and profits.
4. **Support for Unique Applications**: Many manufacturing processes require specialized configurations that are not available in standard spare parts. Custom solutions allow for tailored designs that can cater to the specific needs of unique applications and processes.
5. **Quality Assurance**: Manufacturers of custom-made spare parts often work closely with their clients to understand their specific needs and tolerances. This collaborative approach ensures high-quality production processes and superior materials are used, resulting in parts that require less frequent replacement.
The Process of Custom Parts Manufacturing
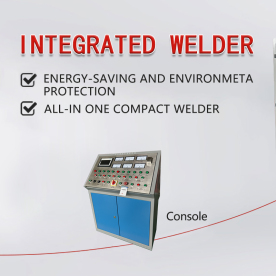
Optimizing Performance and Efficiency with Custom-Made Spare Parts for Solid State HF Welders: The Key to Enhanced Productivity and Longevity
Creating custom-made spare parts for solid state HF welders typically involves several key steps:
1. **Consultation and Assessment**: The process begins with a thorough assessment of the existing machinery and understanding its specific requirements. This often involves discussions with engineers, technicians, and operators to gather insights.
2. **Design and Prototyping**: Once the requirements are understood, engineers will develop designs tailored to fit the exact specifications needed. Often, this includes creating prototypes that can be tested before full-scale manufacturing begins.
3. **Manufacturing**: Using state-of-the-art machinery and technology, the custom parts are manufactured to the precise specifications set out during the design phase.
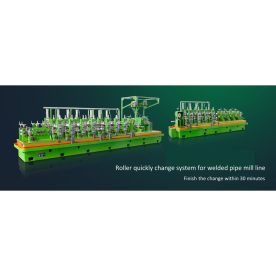
Optimizing Performance and Efficiency with Custom-Made Spare Parts for Solid State HF Welders: The Key to Enhanced Productivity and Longevity
4. **Testing and Quality Control**: Each part undergoes rigorous testing to ensure it meets quality standards and performs effectively within the solid state HF welding system.
5. **Installation and Support**: Many custom parts manufacturers also provide support during the installation process and ensure that technicians are trained to handle the new components effectively.
Conclusion
In today’s competitive manufacturing environments, every aspect of operation must strive for excellence and efficiency. Custom-made spare parts for solid state HF welders not only provide the precise fit and function necessary for optimal performance but also offer significant long-term benefits. By investing in tailored solutions, manufacturers can enhance productivity, reduce downtime, and extend the life of their welding machinery. As the demand for quality and efficiency continues to rise, the importance of custom-made solutions in the welding industry will only grow, making them an essential part of modern industrial operations.Automated pipe mill production line