[Shear&butt welder]Exploring the Versatility and Applications of Shear & Butt Welders in Modern Manufacturing Processes
In the intricate world of manufacturing, the reliance on robust and efficient welding techniques cannot be overstated. Among these techniques, shear and butt welding stands out as a crucial process that enables manufacturers to join materials effectively, particularly in industries such as automotive, aerospace, and construction. This article delves into the intricacies of shear and butt welders, exploring their design, applications, and benefits in modern engineering processes.
**Understanding Shear and Butt Welding**
Shear welding is a process used to join workpieces by applying pressure and generating heat at their interface without the need for filler material. In contrast, butt welding involves bringing two pieces of material edge to edge and welding them together, often using external heat sources, electrical resistance, or friction. The two techniques are frequently combined in applications where structural integrity and strength are paramount.
Welders that specialize in these methods are equipped with advanced technology to ensure precision and reliability. Shear and butt welders can vary in terms of design and functionality, ranging from manual machines to fully automated systems utilizing robotics. The choice of equipment typically depends on the specific requirements of the project, including the materials being welded, the desired joint strength, and the volume of production.
**Applications in Various Industries**
1. **Automotive Industry**: In the automotive sector, shear and butt welders play a vital role in the fabrication of vehicle frames and components. The need for lightweight yet strong materials has led to the adoption of high-strength steel and aluminum, making effective welding techniques imperative. Shear and butt welders provide the precision required for creating strong joints that can withstand the rigors of driving conditions while maintaining overall vehicle integrity.
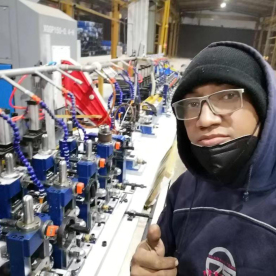
Exploring the Versatility and Applications of Shear & Butt Welders in Modern Manufacturing Processes
2. **Aerospace**: The aerospace industry demands the highest quality standards for safety and performance, and shear and butt welding techniques are employed to meet these rigorous requirements. Whether manufacturing fuselage sections or assembling wing structures, the use of these welders ensures that critical joints are executed flawlessly, contributing to the overall strength and durability of the aircraft.
3. **Construction**: In construction, shear and butt welding is commonly used in the fabrication of steel structures, such as buildings and bridges. By utilizing these welding techniques, construction firms can achieve the high strength-to-weight ratios necessary for modern architectural designs. Additionally, the efficiency of shear and butt welding reduces overall production time, allowing projects to be completed more quickly and cost-effectively.
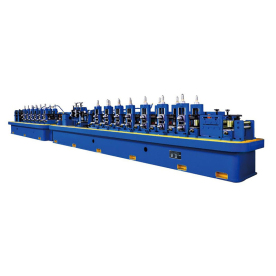
Exploring the Versatility and Applications of Shear & Butt Welders in Modern Manufacturing Processes
4. **Shipbuilding**: In shipbuilding, similar principles apply; shear and butt welders are utilized to construct the hulls and various parts of vessels. The harsh marine environment requires welds that can endure corrosion and mechanical stress, making the strategic application of shear and butt welding critical to vessel longevity and safety.
**Advantages of Shear and Butt Welding**
The benefits of using shear and butt welders go beyond mere efficiency and application specifications. One significant advantage is the quality of the welds produced. Because shear and butt welding creates joints that have minimal heat affected zones, the metal’s properties remain largely unchanged, ensuring strength and reliability.
Further, the automation of these welding processes leads to enhanced productivity. Automated shear and butt welders can operate continuously for long periods, significantly increasing output compared to manual methods. This is particularly advantageous in high-volume manufacturing environments where consistency and speed are essential.
Lastly, the cost-effectiveness of shear and butt welding techniques cannot be overlooked. By reducing the need for additional materials and minimizing waste, manufacturers can keep production costs down while maintaining high-quality standards.
**Conclusion**
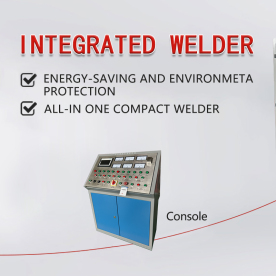
Exploring the Versatility and Applications of Shear & Butt Welders in Modern Manufacturing Processes
In summary, shear and butt welders represent a fundamental aspect of modern manufacturing processes across various industries. Their ability to create strong, reliable joints quickly and efficiently makes them invaluable tools in the quest for quality and durability. As technological advancements continue to evolve in this field, we can expect to see even more innovative applications and improved efficiencies, further solidifying the role of shear and butt welding in the future of manufacturing.Original Spare Parts for Cold Cutting Saw Machines