[Industrial tube making machinery]The Evolution and Future of Industrial Tube Making Machinery: Innovation and Efficiency in Manufacturing
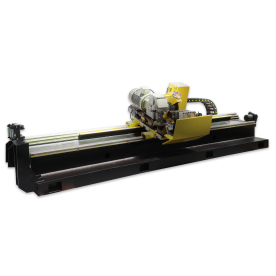
The Evolution and Future of Industrial Tube Making Machinery: Innovation and Efficiency in Manufacturing
****
In the realm of industrial manufacturing, tube making machinery plays a crucial role in producing numerous products used across various sectors such as construction, automotive, and aerospace. The evolution of this machinery over the decades has significantly contributed to enhancing productivity and precision in manufacturing operations. As we delve deeper into the advancements in industrial tube making machinery, we examine its history, technological innovations, and what the future holds for this essential equipment.
Historically, tube making began in the late 19th century when craftsmen used rudimentary tools to shape metal into tubes. Early machines were often manual and limited in what they could produce. However, as industrialization took hold, the demand for metal tubes surged, leading to the need for more efficient and automated machinery. The introduction of electric motors and hydraulic systems transformed tube making, allowing for greater speeds and precision.
Today’s industrial tube making machinery represents a pinnacle of engineering with continuous advancements in technology. Modern machines are equipped with computer numerical control (CNC) systems that enable high degree of automation and precision. This allows manufacturers to produce intricate designs and specifications that were not feasible with earlier technology. CNC technology has remarkably reduced human error and increased efficiency, allowing for mass production without sacrificing quality.
One of the most notable advancements in tube making machinery is the integration of robotics. Automation through robotics has enhanced production capacities, reducing labor costs and the time taken to produce components. Robotic arms can perform tasks such as loading, unloading, welding, and cutting with precision unmatched by human operators. This not only improves the overall speed of the production line but also enhances workplace safety by minimizing the risk of accidents associated with manual handling.
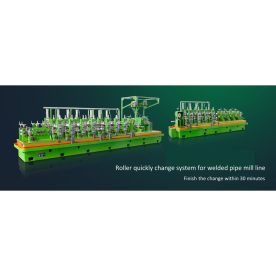
The Evolution and Future of Industrial Tube Making Machinery: Innovation and Efficiency in Manufacturing
Another significant trend influencing the industrial tube making machinery landscape is the demand for sustainable manufacturing practices. As industries face increasing pressure to reduce their carbon footprints, manufacturers are investing in energy-efficient machines and processes. Advanced machinery now incorporates systems that monitor energy consumption in real-time, allowing operators to optimize performance and reduce waste. Furthermore, innovations such as tube recycling systems and eco-friendly lubricants are gaining traction, promoting sustainability in tube production.
The customization of tube making machinery is also vital in today’s market. With the rise of diverse industries requiring specific tube dimensions and materials, manufacturers are increasingly seeking equipment that can be tailored to meet their unique needs. Modular designs that allow for easy reconfiguration are becoming popular, enabling businesses to adapt in real time to changing market demands. This flexibility not only ensures that manufacturers remain competitive but also enhances their capacity to innovate and develop new products.
Looking ahead, the future of industrial tube making machinery is poised for exciting developments. One emerging trend is the Internet of Things (IoT), where machinery is connected to the internet for predictive maintenance and data analytics. By monitoring machine performance and health in real-time, manufacturers can anticipate breakdowns before they occur, thus minimizing downtime and maximizing productivity.

The Evolution and Future of Industrial Tube Making Machinery: Innovation and Efficiency in Manufacturing
Artificial intelligence (AI) is also expected to play a significant role in the future of tube making. Smart algorithms can analyze production patterns, suggest optimizations, and even manage supply chain logistics more effectively. This level of interconnectivity and intelligence is likely to create a more agile manufacturing environment, capable of responding swiftly to market changes.
In conclusion, industrial tube making machinery has evolved dramatically over the past century, driven by technological advancements and changing market demands. From its manual beginnings to the automated and highly efficient systems of today, the industry has continually adapted to enhance productivity and quality. As we surge into a new era of innovation, incorporating IoT and AI into tube making machinery, the possibilities for efficiency and sustainability are boundless. Manufacturers who embrace these changes will not only thrive in today’s competitive landscape but also set the standards for future production practices.Customized pipe mill production line solutions