[Solid state HF welder for thin metal sheets]Revolutionizing Metal Fabrication: The Impact of Solid State HF Welder for Thin Metal Sheets in Modern Manufacturing
In recent years, the manufacturing industry has seen significant advancements in welding technologies, leading to improvements in efficiency, quality, and versatility. Among these innovations, the solid-state high-frequency (HF) welder has emerged as a game-changer, particularly in the welding of thin metal sheets. This article explores how solid-state HF welders are revolutionizing the fabrication processes, enhancing the performance of traditional welding techniques, and addressing the challenges associated with thin metal sheet welding.
Understanding Solid State HF Welding Technology
To appreciate the impact of solid-state HF welders, it’s essential to understand the technology behind them. Traditional welding methods, such as arc or resistance welding, often struggle with thin materials due to the high heat levels that can cause warping or burn-through. Solid-state HF welding, however, utilizes high-frequency electromagnetic fields to create heat, which offers precise control over the welding process.
The solid-state design employs semiconductor devices, which allow for better energy management, higher efficiency, and a more compact footprint compared to conventional vacuum tube systems. By generating heat directly within the material, solid-state HF welding minimizes the risk of damage to the surrounding area, making it particularly suitable for thin metal sheets often used in industries such as automotive, aerospace, and electronics.
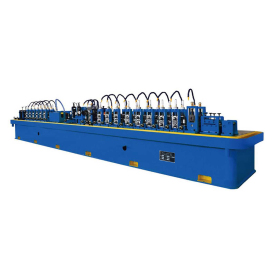
Revolutionizing Metal Fabrication: The Impact of Solid State HF Welder for Thin Metal Sheets in Modern Manufacturing
Advantages of Using Solid-State HF Welders for Thin Metal Sheets
1. **Precision and Control**: Solid-state HF welders provide excellent control over the welding parameters. Manufacturers can adjust the power, frequency, and duration of the weld with precision, ensuring optimal results for various metal thicknesses and types. This feature is critical when working with thin metal sheets, where even slight deviations can lead to defects.
2. **Reduced Heat-Affected Zone**: One of the significant advantages of solid-state HF welders is the limited heat-affected zone (HAZ). The focused heat generation means that the area surrounding the weld remains cooler. As a result, this reduces the risk of warping, distortion, and structural integrity loss, which are common issues faced when welding thin materials.
3. **Faster Production Rates**: The rapid heating and cooling cycles achievable with solid-state HF welding lead to shorter cycle times. This increased speed not only boosts production efficiency but also enhances overall productivity, allowing manufacturers to meet tight deadlines without compromising on quality.
4. **Lower Energy Consumption**: Solid-state technology is known for its energy efficiency. By utilizing less power than traditional welding systems, manufacturers can reduce their operational costs and minimize their environmental footprint. This aspect is increasingly important in today’s manufacturing landscape, where sustainability is a growing concern.
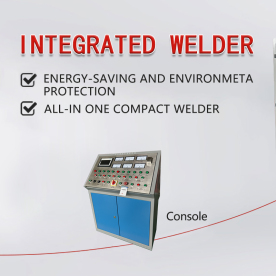
Revolutionizing Metal Fabrication: The Impact of Solid State HF Welder for Thin Metal Sheets in Modern Manufacturing
5. **Versatility**: Solid-state HF welders are compatible with a wide range of materials, including metals like aluminum, copper, stainless steel, and more. This versatility makes them an attractive choice for manufacturers who work with various alloys in thin sheet applications.
Applications in Different Industries
The versatility and efficiency of solid-state HF welders make them suitable for various industries relying on thin metal sheet fabrication. In the automotive industry, for instance, manufacturers utilize this technology for welding parts and components like battery enclosures and chassis elements. The aerospace sector benefits from the high-quality welds necessary for aircraft components, which must meet stringent safety and performance standards.
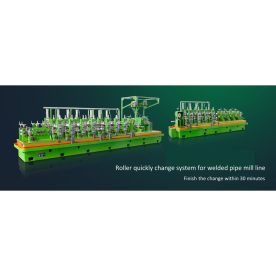
Revolutionizing Metal Fabrication: The Impact of Solid State HF Welder for Thin Metal Sheets in Modern Manufacturing
In electronics manufacturing, solid-state HF welders are used to produce thin metal enclosures and other components that require precise welding without compromising the material’s integrity. In every case, the ability to deliver strong, reliable welds with minimal heat impact on the surrounding areas gives manufacturers a significant edge over traditional welding technologies.
Conclusion
As the demand for lightweight, high-strength materials continues to grow across various industries, solid-state HF welders are adapting to meet these needs effectively. Their ability to provide precise, efficient, and reliable welds in thin metal sheets marks a significant advancement in manufacturing technology. As manufacturers embrace the advantages of this innovative welding technique, we can expect to see a transformation in metal fabrication processes, driving efficiency, quality, and sustainability in the industry. The future looks bright for solid-state HF welding, paving the way for further innovations in welding technology and expanding the possibilities for engineering and manufacturing.Multi-functional tube making machine